SERENO
REDEFINING PERFORMANCE, PRECISION, AND FLEXIBILITY
Sereno Etch & Clean
Redefining Performance, Precision, and Flexibility for Wet Etch & Clean Processes
01 SERENO at a glance
Single Wafer Wet Etch & Clean Multichamber Equipment
SERENO IS A HIGH-THROUGHPUT WET CHEMICAL SURFACE TREATMENT EQUIPMENT PLATFORM DESIGNED FOR EFFICIENCY AND VERSATILITY. IT COMBINES THE UNIQUE PERFORMANCE BENEFITS OF SINGLE-WAFER TECHNOLOGY WITH A MODULAR, COMPACT DESIGN, DELIVERING THE LOWEST COST OF OWNERSHIP WHILE MAINTAINING MAXIMUM FLEXIBILITY.
With its versatile design, SERENO is tailored to meet the specific needs of FEOL and BEOL wet etch and clean applications where tight etch uniformity and high particle removal efficiency (PRE) are paramount.
SERENO addresses critical challenges in wet chemical surface treatment, including yield loss from poor uniformity and high chemical consumption typically seen in legacy batch processes.With an innovative chemical scan and dispensing system, integrated metrology, and onboard chemical supply, SERENO provides precise, recipe-based, and adaptable wafer surface treatment for 6“, 8“, and 12“ substrates, significantly enhancing uniformity and yield while reducing waste and ownership costs.
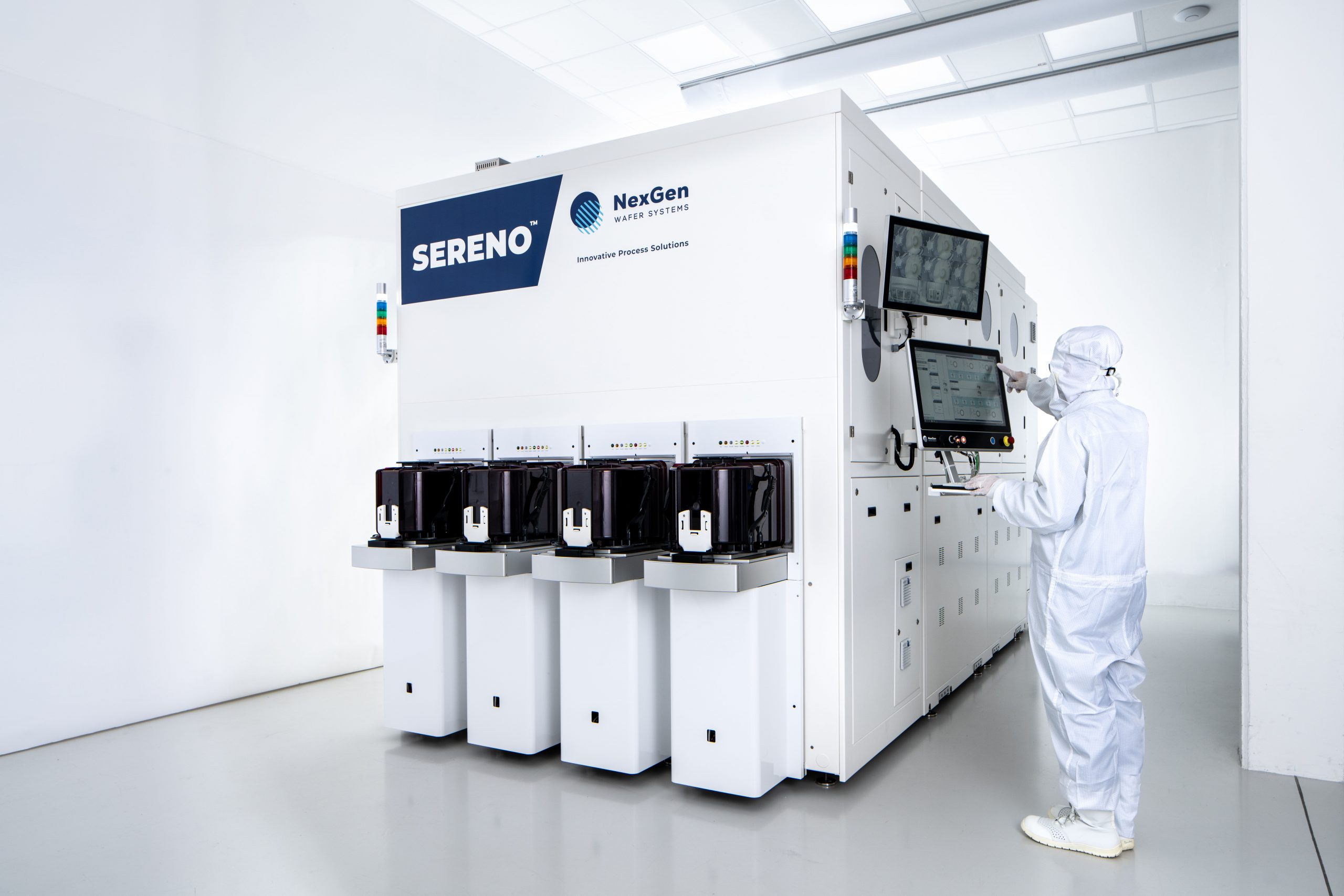
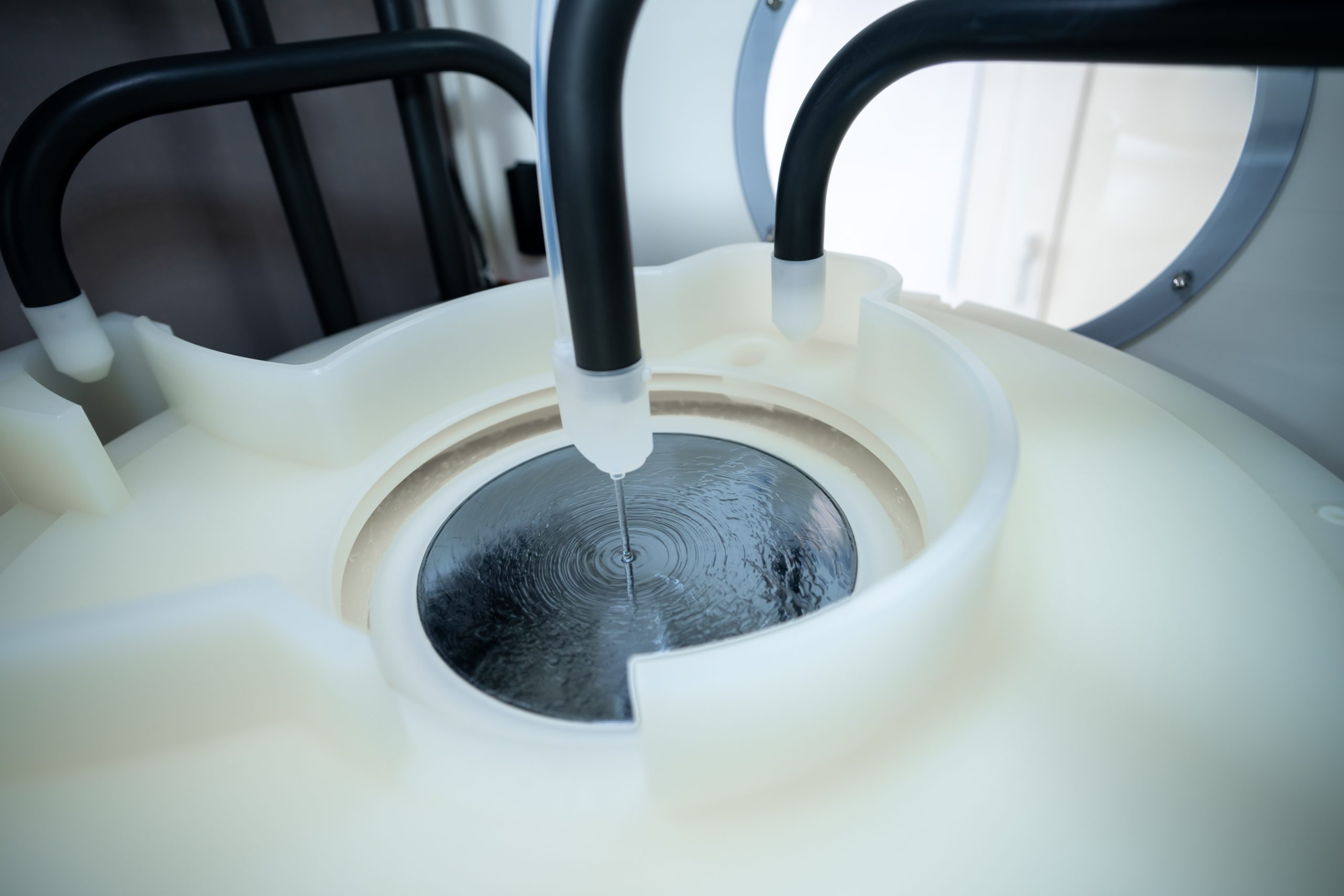

Elevate your etch and clean performance
SERENO IS A HIGH-THROUGHPUT WET CHEMICAL SURFACE TREATMENT EQUIPMENT PLATFORM DESIGNED FOR EFFICIENCY AND VERSATILITY. IT COMBINES THE UNIQUE PERFORMANCE BENEFITS OF SINGLE-WAFER TECHNOLOGY WITH A MODULAR, COMPACT DESIGN, DELIVERING THE LOWEST COST OF OWNERSHIP WHILE MAINTAINING MAXIMUM FLEXIBILITY.
With its versatile design, SERENO is tailored to meet the specific needs of FEOL and BEOL wet etch and clean applications where tight etch uniformity and high particle removal efficiency (PRE) are paramount.
SERENO addresses critical challenges in wet chemical surface treatment, including yield loss from poor uniformity and high chemical consumption typically seen in legacy batch processes.With an innovative chemical scan and dispensing system, integrated metrology, and onboard chemical supply, SERENO provides precise, recipe-based, and adaptable wafer surface treatment for 6“, 8“, and 12“ substrates, significantly enhancing uniformity and yield while reducing waste and ownership costs.
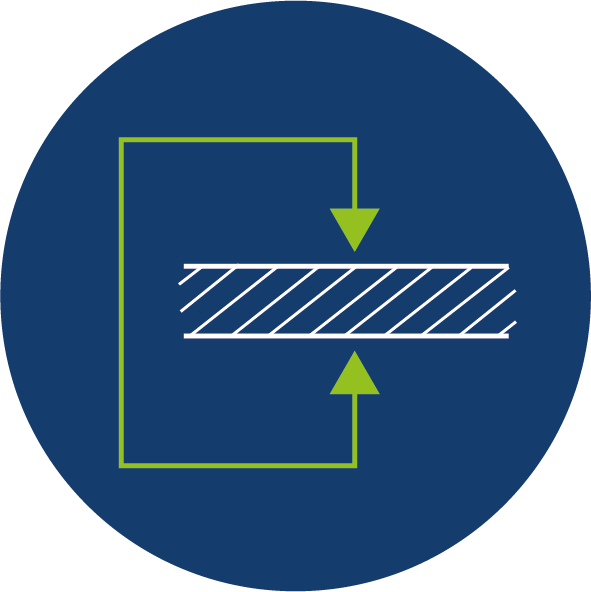
Integrated Metrology
Provides real-time measurement and control of critical process parameters on integrated measurement stages, enabling precise, repeatable thickness and surface roughness measurements.
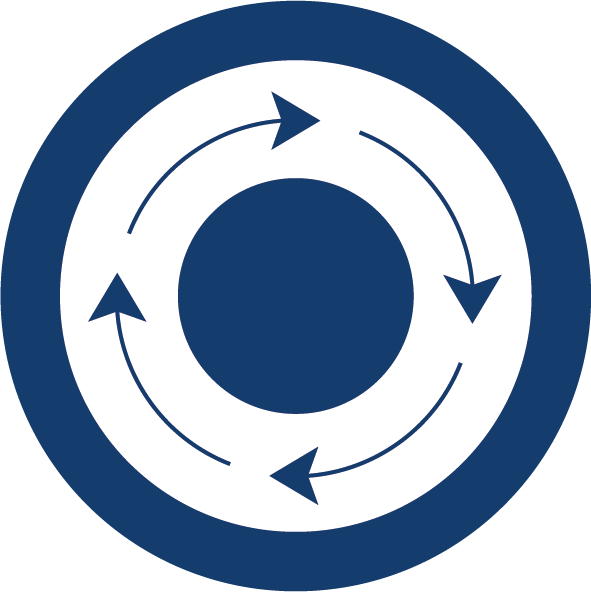
High-Performance Process Chambers
Deliver stable airflow and chemical flow for a robust, repeatable process, ensuring optimal wafer results.
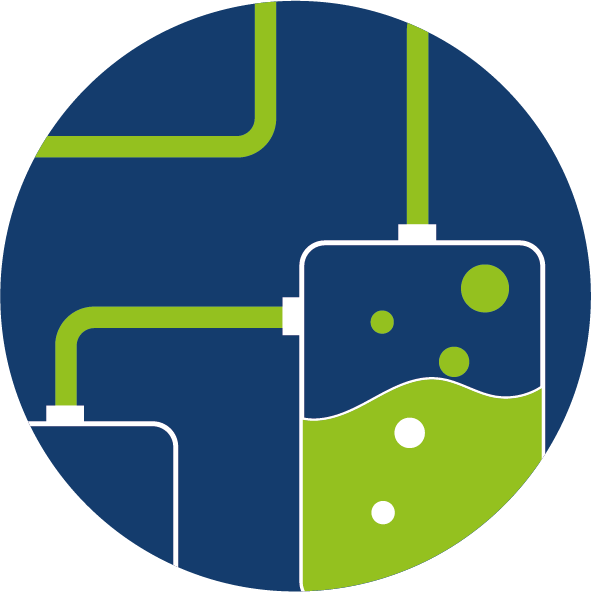
Onboard Chemical Supply
Mixes and conditions up to three process chemicals for reclaim and single-stream processing.
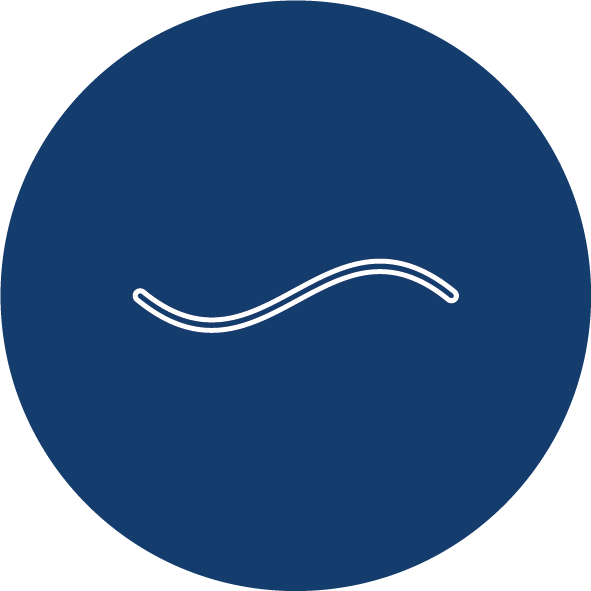
Ultra-Thin Wafer Processing
Contactless Bernoulli Handling system supports processing extremely thin, fragile substrates and substrates with high bow and warp.
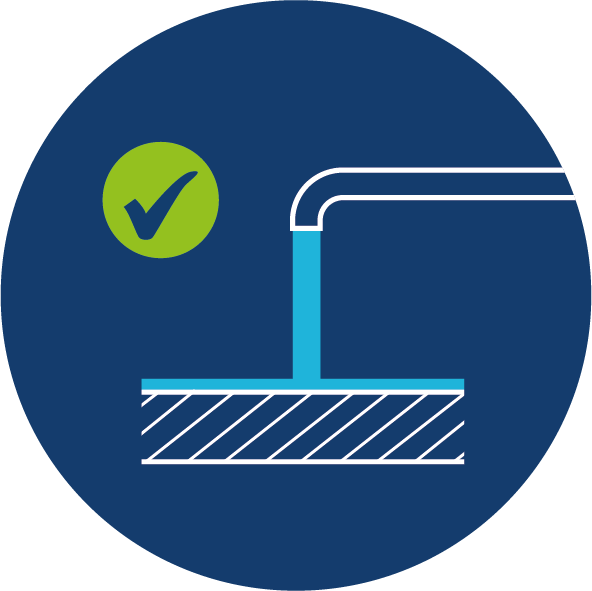
Innovative Dispensing Control
Best-in-class uniformity and yield with maximum degrees of freedom through customizable scan and dispensing profiles.
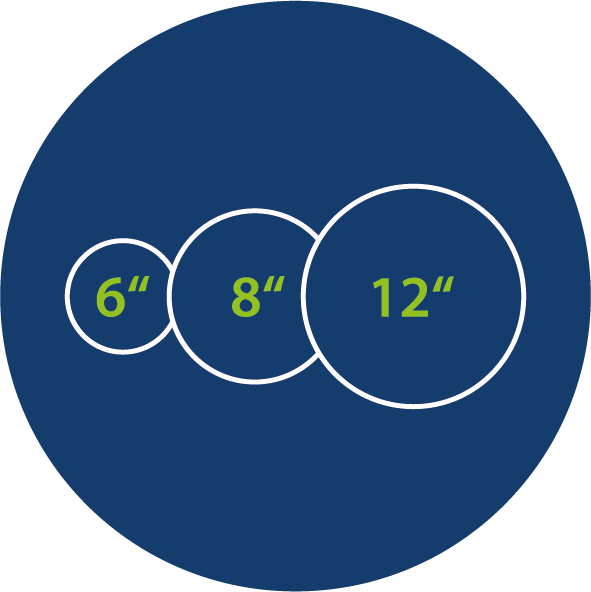
Maximum Flexibility
Supporting 6“, 8“, and 12“ wafers and multiple substrate types as well as bridge tool functionality for simultaneous processing of two wafer sizes.
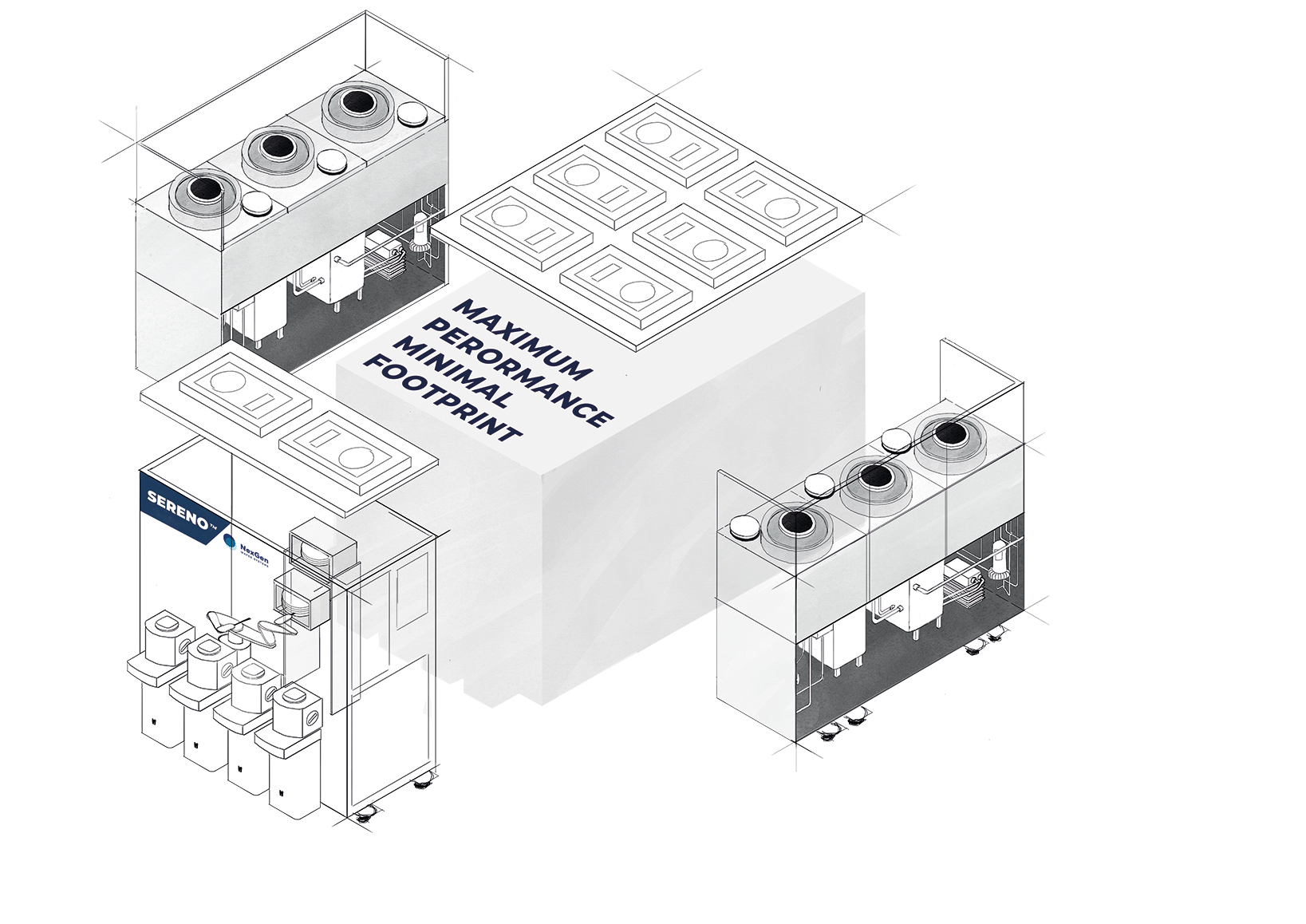
EFFICENCY AT ITS BEST
SERENO EXCELS IN BOTH WAFER THROUGHPUT AND FLOOR SPACE EFFICIENCY, OFFERING A COMPACT, HIGH-PERFORMANCE EQUIPMENT SOLUTION WITH A HEIGHT OF LESS THAN 2.8 METERS. THIS MAKES IT IDEAL FOR SEAMLESS INTEGRATION INTO FABS WITH LOW CEILING HEIGHTS, ENSURING OPTIMAL PERFORMANCE EVEN IN SPACE-CONSTRAINED ENVIRONMENTS.
02 applications
Surface Clean
Film & Metal Etch
Substrate Etch
ONE PLATFORM, THREE CONFIGURATIONS
To meet diverse process requirements, the SERENO platform offers three distinct configurations, each optimized for a specific application group: Surface Clean, Film and Metal Etch and Substrate Etch.
With three configurations available via one single, versatile platform, SERENO empowers you to handle a broad range of process applications. It provides an adaptable solution that meets today’s challenges while preparing for future demands.
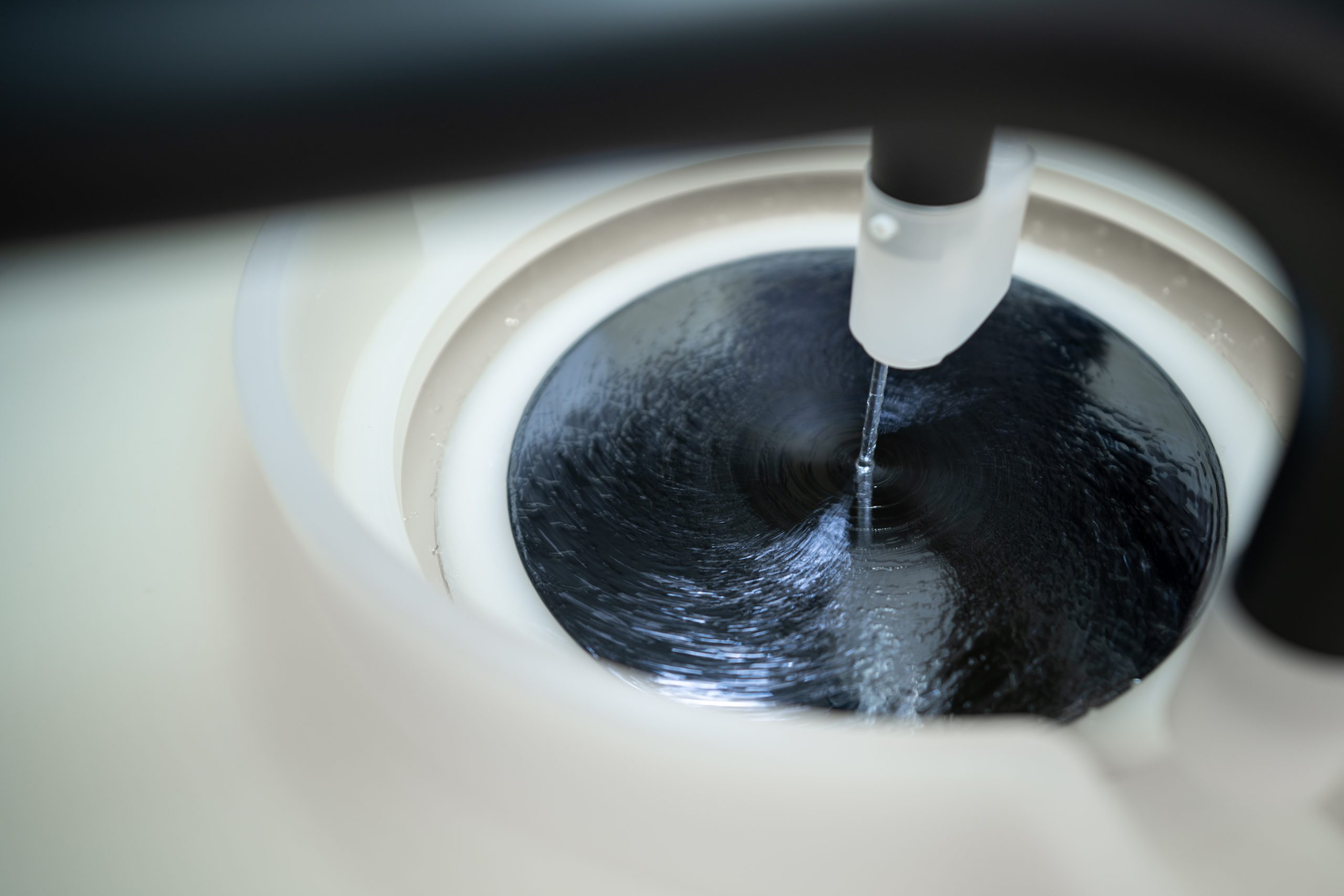
Polymer removal
Residual removal
Incoming wafer cleaning
(Silicon Nitride | Silicon Dioxide | Polysilicon)
Metal Etch
(Ti | Ni | Ag | Au | Al | W | Cu …)
UBM
(Ag | Ni| Ti …)
Stress relief
Surface conditioning
Vias reveal
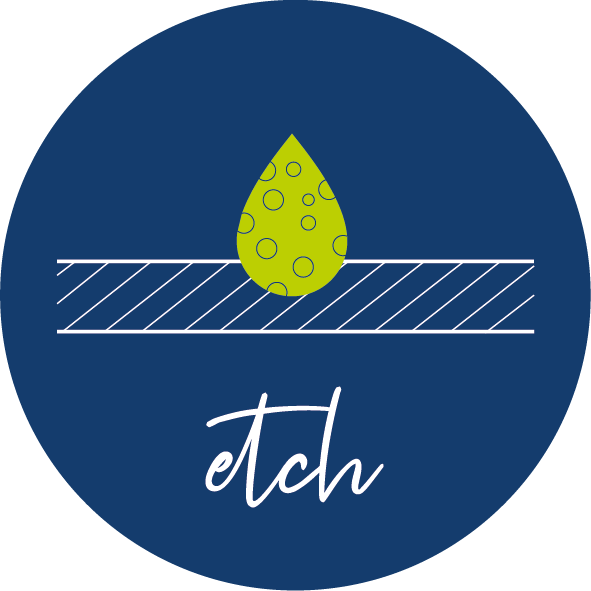
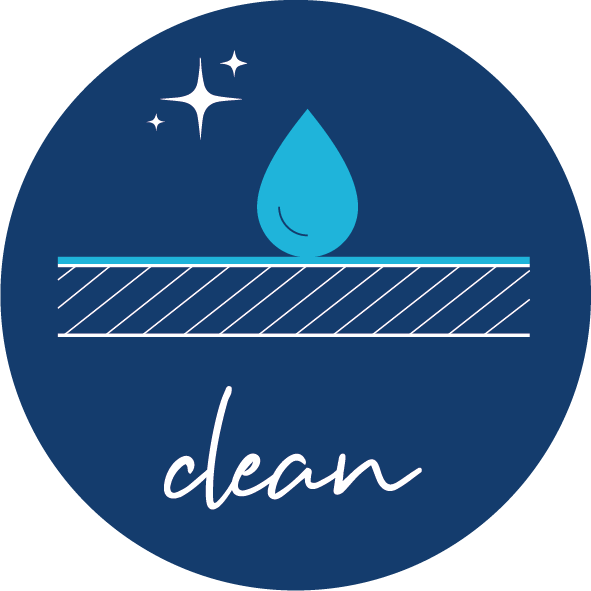
We provide novel Etch & Clean Solutions
SURFACE CLEAN
FILM & METAL ETCH
SUBSTRATE ETCH
SUPPORTED SUBSTRATE TYPES
Si /// SiC /// GaN /// GaAs /// Al2O3 /// ZnO
6“, 8“, 12“
03 integrated metrology
Advanced Metrology for Precision and Yield Optimization
1. Integrated Thickness
Measurement and Control:
This feature is particularly beneficial for substrate etch applications, where target thickness, within-wafer uniformity, and Total Thickness Variation (TTV) are critical to maintaining product integrity. SERENO’s real-time thickness control ensures that these parameters remain within specification, preventing costly rework and improving overall process efficiency for every wafer.
2. Integrated Roughness
Measurement and Control:
For applications where surface smoothness is paramount, such as polish or rough surface conditioning, SERENO offers integrated roughness measurement. This system guarantees tight control over within-wafer roughness uniformity, enhancing device performance by maintaining consistent surface properties across each wafer while reducing chemical consumption.
3. Endpoint Detection (EPD):
SERENO’s advanced Endpoint Detection (EPD) system automatically detects layer transitions, ensuring optimal process control when layer selectivity is crucial. EPD helps avoid over-etching or under-etching by precisely halting the process at the correct moment, improving process robustness and consistency, especially in multi-layer and complex etch applications.
4. Onboard Chemical Concentration Monitoring and Control:
Tight chemical concentration control is essential in wet etch and clean processes to ensure repeatability and precision. SERENO’s built-in Chemical Concentration Monitoring and Control allows for real-time adjustments, minimizing chemical waste and ensuring consistent process outcomes. This feature is vital for maintaining optimal etch rates and uniformity, leading to a more reliable process overall.
04 sustainability
Eco-friendly manufacturing with real-time data
By providing real-time data on material and utility consumption, SERENO enables fabs to actively monitor and adjust their processes to achieve environmental goals while simultaneously reducing operational costs. The platform is an ideal solution for manufacturers seeking to balance high productivity with sustainability through data-driven decisions.
Our Commitment to Quality, Safety, and Sustainability
NexGen Wafer Systems holds ISO 9001 certification for quality management, underscoring its commitment to delivering reliable, customer-focused products and services, and ISO 14001 certification for environmental management, emphasizing ongoing efforts to reduce environmental impact. CE marking ensures compliance with EU safety, health, and environmental standards, allowing distribution across the European Economic Area. Compliance with SEMI S2, S8, and S22 standards guarantees strict adherence to safety, ergonomics, and environmental guidelines. Additionally, NexGen supports full integration with Automated Material Handling Systems (AMHS), providing interfaces for AGV and OHT systems to enhance process control and product yield.
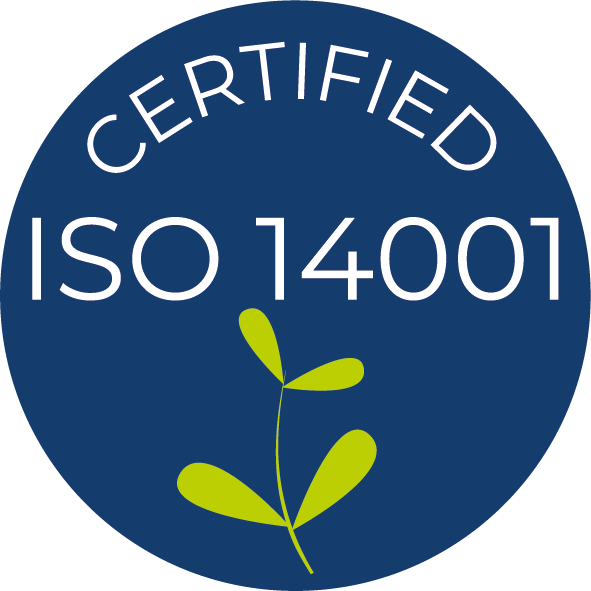
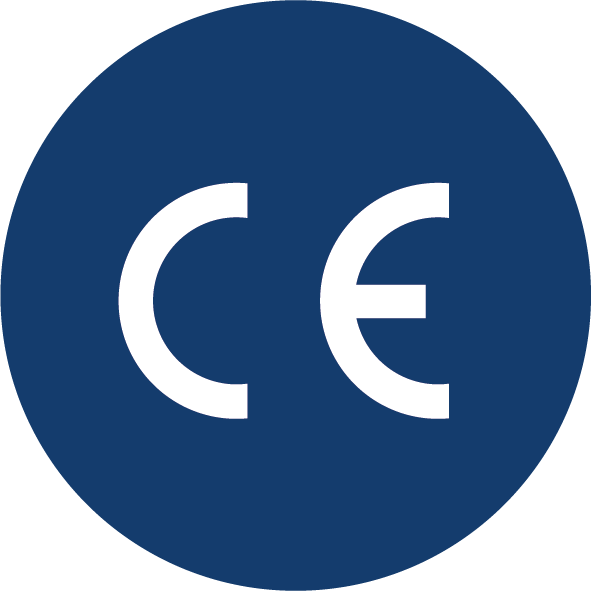
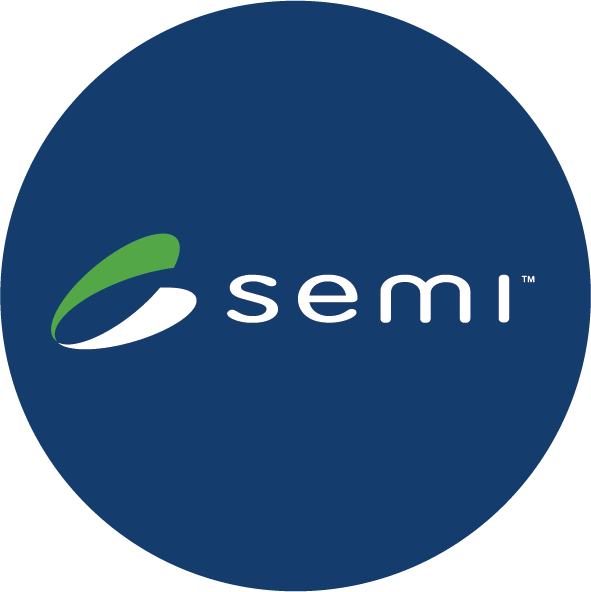
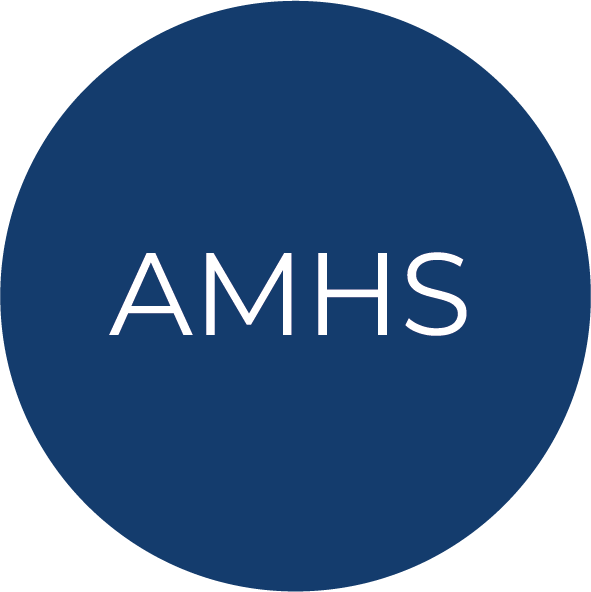